Front
Frame, Engine, Suspension and Brakes
Remove old frame and paint bulkhead
Install new frame and engine Fit
front suspension and brakes Install Alternator
Rear Frame, Engine, Suspension and Brakes Remove
rear floor section Install rear reinforcement
frame Install modified frame and engine
Fit rear suspension and brakes
Install rear firewall
Front\Rear Clutch and Gearbox Linkages Modify
Vauxhall Gear Linkage to be correct length
Install at correct height for end of shaft to be parallel with gearbox
pivot point Install clutch slave cylinders
Remote rear gearbox engage pin
Clutch and Brake Master Cylinder Pedal Box Assembly
Create pedal box assembly Install
in car and attach to mini pedal setup Install
clutch and brake lines
Electrical System (excluding engine management)
Create \ Install new Fuse\Relay Panel
Create \ Install new loom
Install car battery
Traction Control (only when running both engines)
Front \ Rear Wideband Comtrollers
Front and Rear Engine Cooling\Heater Installation Run water piping from front to rear of car
Install front engine expansion tanks
Install front\rear radiators with fan
Install radiator fan cowling
Install Air Ducting to Rear Valance Panel
Install rear engine expansion tank
Create\install new heater core
Front Engine QED Throttle Bodies and DTA
Management Install QED Throttle Bodies
Install adjustable fuel pressure regulator
Install fuel pump and fuel lines Install
DTA ECU and associated wiring
Dashboard
Installation Create dashboard inner
framework Create outer panels \ switch panels
Install dashboard components
Handbrake Installation
Install handbrake cable calipers
Route handbrake cables from handbrake lever to calipers
Cosmetic Changes to Interior\Exterior
Install extended wheel arches
Install racing seats
Install racing harnesses
General Engine\Gearbox Upgrades
Install Uprated Rods
Install Pocketed Pistons
Install Uprated Main\Big End Bearings
Install Uprated Oil Pump
2.5" Stainless Exhaust Systems
Quaife ATB for front gearbox
Rear Engine QED Throttle Bodies and DTA Management Installation
Install QED Throttle Bodies
Install Adjustable Fuel Pressure Regulator
Install fuel pump and lines Install DTA ECU and
wiring
Nitrous Oxide Installation
Install Nitrous Bottle
Install Rear Nitrous\Fuel Pulsoids
Install Distribution Block and Crossfire Injectors
Install Throttle Activation Switch
Nitrous Bottle Heater and Pressure Gauge
General Bits'n'Bobs that don't fit into any particular
category
Washer Bottle Installation
Wiring \ Pipe Tidying
Cut Slick Tyres
Uprated Springs
Stronger Engine Mounts
Fire Extinguisher
Heated front windscreen
Extra rear speakers
|
I came across a mini estate for sale which already had
one AMT 16V frame fitted to the front which removed a lot of the front
end work effort and also saved me having to order another AMT frame as
the original one I was planning to use was already on order.
The existing frame was quite old and would require a strip down and
repaint before use.
(Click on pictures to see larger version)
Front
Frame, Engine, Suspension and Brakes Installation
I removed the old AMT frame and all ancillaries on the bulkhead then
painted with copious amounts of hammerite to try and fend off the rust
demon. :)
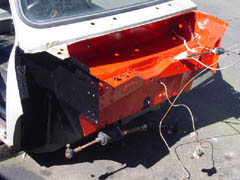
This is the new AMT frame mounted and the first engine dropped into
place. Also same install with front end placed on which shows just
how tight the final result will be.
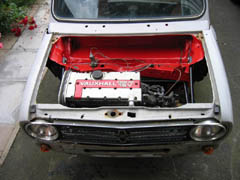
The front metro
turbo brakes are also now in place. Found that the AVO Coilover
Shocks didn't have a large enough hole for the mount bolts to fit so had
to drill them out and the kit didn't come with any spacers to remove the
play in the upper and lower mounts so some spacers were made out of
nylon bar. The upper arm has been adjusted to 6.75" with the upper
tie bar set to make this arm 90 degrees to the frame. (The lower arm and
tie bar will be setup at a later date) I may change the calipers
to some alloy ones at a later date to save some weight as the cast ones
are really heavy.
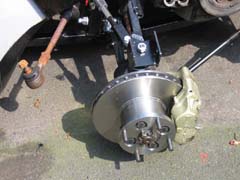
There isn't enough space to install the alternator in
the standard Vauxhall location at the rear of the engine so new brackets
had to be made to place the alternator at the front.
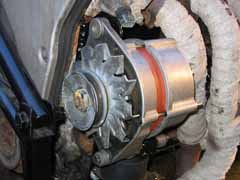
Rear Frame, Engine, Suspension and Brakes Installation
This is where the real work began as a lot of the basic
front work was already completed.
Firstly a large section of the rear floor was removed to
enable space to install the modified AMT frame and engine with the
wheels still centered within the arches. After much measuring of the
front frame, mounts and suspension it lined up well with the AMT frame
front alloy crossmember mount points sitting just ahead of the rear bulkhead. A
large portion of the rear bulkhead had to be removed so extra
strengthening is to be added on the floor later. A section of the rear
arches was also removed to allow space for the suspension arms and the
coil over shocks.
The rear floor would now be the bolting point of the
mounts which usually fix just below the front bulkhead at the front of
the floor pans on the driver and passenger side. The rear floor
was way too flimsy to be able to withstand any load of this type so a
subframe was constructed to fit below the remaining rear floor.
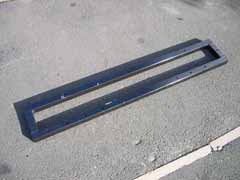
The back mounts on the AMT frame, which bolt to the
footwells, were too low to attach to the rear floor so they were removed
and raised approx 4 inches to connect just above the lower arm mount
point. The engine was installed into the frame before fitting to
the car as it would be hard to install when the frame was in place. The front alloy crossmember mounts are connected to
the rear firewall with some reinforcement to stop the floor tearing.
With the rear floor subframe installed you can jump on the rear floor
and no flex is visible.
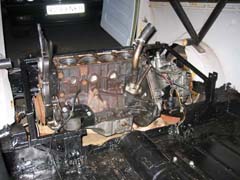
The top mounts are bolted to the main cross member of
the AMT frame and also at the front of the frame where the extra brace
bars are normally installed. The sides of this assembly are then
attached to the remaining cross member portion of the rollcage. By
utilizing 3
different mount locations on the rear frame to spread the torsional
stresses i'm hoping it will be strong
enough to take the load without too much shell flex at any one point. This frame section
also holds the mount points for the rear coilovers, by using this as the
rear suspension mount it will hopefully relieve the body of the extra
stress of the rear suspension load.
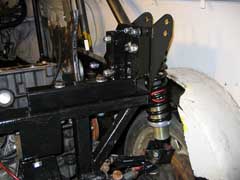
Again the upper arms were set to 6.75" and the tie bar
set to make the upper arm 90 degrees to the frame. The wheels sit
quite centered in the wheel arches already, this position should be
somewhat adjustable as no steering is required on the rear so the
upper\lower arms should be ok to adjust to make the wheels sit more
forward\backward as required (I have moved the spacers on the upper arm
so that they are both to the rear of the mount point, this has moved the
upper arm approx 5mm forwards without then affecting the angle of the
arm to the frame by adjusting the tie bar). The brakes are currently identical to the
front setup (metro turbo setup) but I will need to either add an extra
pair of calipers for the handbrake or install some
alloy 2 pot calipers with handbrake cable function to make passing the
MOT a little easier as the parking brake needs to be independent of the
main braking system hydraulics.
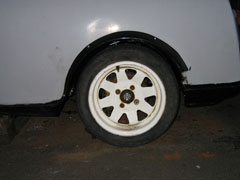
As it was basically a front setup at the rear it would
need locked off steering arms, these would provide the rear toe
adjustment but had to be located so as to minimize any bump steer
effect. After testing many mount points this mount point was
chosen as it doesn't show any bump steer through min-max suspension
travel. I've now added a cross beam and sleeved the mount points
to add quite a lot of strength and eliminate any flexing issues.
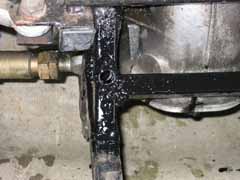
Required for the MOT and also my own peace of mind was
to separate the rear engine from the front cabin. I was originally
planning on an aluminum cover to seal the rear engine out of sight but
this was removed as it was just too difficult to seal properly, didn't
offer much in the way of noise reduction and also people were
complaining they couldn't see the rear engine at shows etc. In
light of this I have
opted to construct a firewall between the rear engine and the front
cabin area. It has been constructed from 3/4" MDF and 5mm
Polycarbonate.
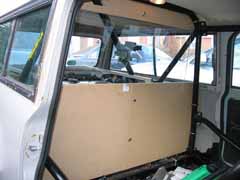
Front\Rear Clutch and Gearbox
Linkages
The standard Vauxhall gear linkage is way too long for
the mini so had to be shortened about a foot. I decided that
rather than have the main adjustment right on the pivot point, which is
hard to get to, I'd make it adjustable nearer the gearstick itself.
The gearstick assembly needs to be installed at the correct height so
the shaft runs parallel to the floor as per the standard Vauxhall
installation..
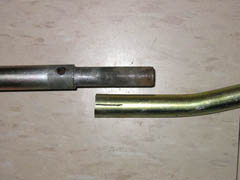
Finally got round to installing the gear linkage in the
car, had to cut down the pivot bar that fits on the rear engine mount
and also needed to knock a big dent in the bulkhead so the pivot bar
would move enough to get 1st and reverse gears. Surprisingly the
gear setup worked at the first attempt with all gears available and no
messing to get 5th and reverse both to work at the same time. The
gearstick is mounted approx 2-3 inches above the transmission tunnel on
an aluminium box section to ensure the linkage bar was parallel to the
floor.
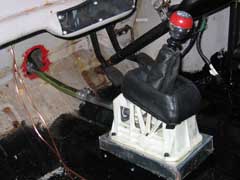
While a cable clutch would be the simplest to install
for the front engine it wouldn't be so easy to get a cable to reach the
rear engine so I decided on hydraulic instead. Upon measuring a
standard Vauxhall install I found that approx 30mm of travel is required
to operate the clutch lever on the F20 gearbox. The old style
horizontally mounted mini slave cylinders have a max travel of approx
40mm so would be suitable to use to push the clutch lever rather than
pull with a cable. A suitable mounting place was not available for a simple bolt on
so one had to be constructed to suit which bolts to the engine
mount point and the side of the gearbox.
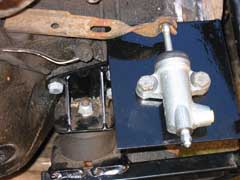
The rear gearbox linkage would be much more difficult
and I decided rather than use a solid bar assembly (which would be quite
a mess in the car) I would use a cable setup. The cables are a
special push\pull type which are capable of handling approx 70kg of
forward\backward force (these same cable types are used in several high
performance kit cars so should be ok).
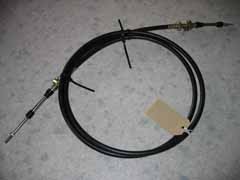
Connecting these cables from the front gear linkage
would be quite difficult though as it rotated as well as moved
back\forth. I also wanted to be able to disconnect the rear link
so the front engine was available for general traveling around to save
on fuel costs.
The first cable to install was the forward\backward
motion cable, this is the one which needed to have the simple disconnect
option. I decided the best way to achieve this was to make a
sleeve which fitted over the front gear linkage which would push the
cable forward\backward but be able to swivel on the shaft so the
left\right movement didn't affect the cable position. I used a
removable pin in the assembly to achieve the required simple disconnect
option.
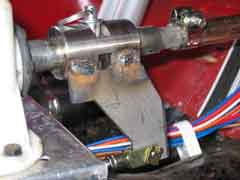
The gear selector on the F20 gearbox has been modified
to face the other way as getting the cable all the way around would have
been problematic.
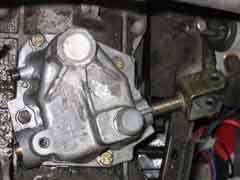
I modified the rear engine mount which contained the
gearbox linkage pivot bar so it could be installed on the other side of
the gearbox with a custom bracket which linked with the clutch cylinder
bracket and then chopped the pivot bar so it was at approx 90 degrees
rather than straight in order to get the cable to connect and push\pull
from the side rather than direct from in front. This is now
working correctly and I can get 3rd\Neutral\4th in unison with the front
gearbox. The bracket holding the cable in place is bolted to the
gearbox housing so should be quite secure.
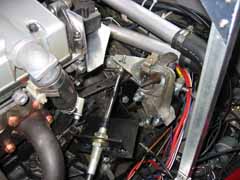
The cable required for left\right twist motion would be a little more
difficult to install as I didn't want to lose too much footwell space on
the passenger side (I initially wanted to install this cable connected
to the gearbox link directly but found insufficient room to fit it in.
Eventually I found this location a good compromise and only lost a few
inches of footwell space.
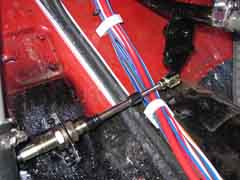
The left\right twist connection on the rear engine itself would also
prove difficult, with so many wires, water pipes and fuel pipes there
was very little room remaining. Once installed I also had problems
getting 5th and rev on the front engine, I think this was due to
increased load on the gearstick shaft causing some flex somewhere.
I good attack of the Vauxhall gearstick cage allowed just enough extra
left\right movement and now all gears are available.
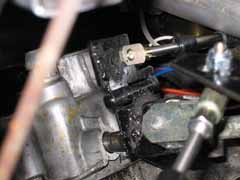
I've noticed that the rear linkage brackets were able to
flex sometimes if the gear wanted to be a little difficult resulting in
the front engine gear being engaged but the rear gear remaining not
completely engaged but you wouldn't be able to feel this from the
gearstick which resulted in many messed up 1/4 mile attempts. To
counter this I have added a couple of extra brackets onto the mounts and
this has removed all visible flex and the shift feels much more solid
and if a gear doesn't want to go in you can feel this now in the
gearstick.
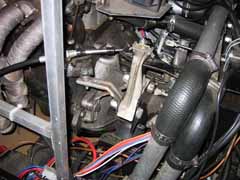
Since completing most of the dashboard it's become
difficult to reach the engage pin to engage\disengage the rear gearbox
linkage. To work around this I have mad a remote control for the
pin to be removed\installed using one of the mini choke control cables
to lever the pin in and out of the linkage assembly.
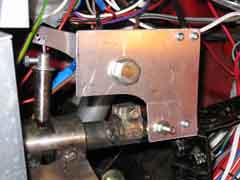
Clutch and Brake Master Cylinder Pedal
Box Assembly
As I was using 4 pot calipers front and rear along with
2 clutch slave cylinders there wasn't really any option but to make my
own master cylinder pedal box assembly.
This has been the hardest part to make so far but i'm
pleased with the result (if it works of course when I get the car on the
road) :o)
There are 2x 0.625" master cylinders for the front and
rear brakes and a balance bar assembly to provide brake split adjustment
front\rear. I also have 3 mount points on the input bar so can
adjust the pedal ratio to increase or decrease required pedal travel \
pressure. For the clutches I have used 2x 0.75" master cylinders
as the stock mini master cylinder was 0.75". Each clutch can be
adjusted separately on the master cylinders and again I have made
allowances to be able to adjust the pedal ratio to increase\decrease
maximum clutch travel. The pipework for the brakes and clutches
was a nightmare :)
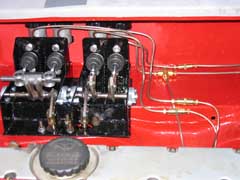
Electrical System (excluding engine
management)
The existing electrical system in the mini was a
complete mess so I decided to install a new modernized electrical setup
rather than try and plumb into the existing relays, fuses and wiring.
The job ended up being much more complex than I had
originally thought, over 30 hours was spent just designing and
documenting the electrical system to replace the entire mini setup
apart from the wiper \ indicator stalks, ignition switch and physical
lights.
Instead of small pockets of fuses \ relays I purchased a
modular fuse \ relay panel which could be built up in parts to suit the
application. Most main power requirements are now relay fed rather than
just through the switches and stalks.
This is a picture of the relay \ fuse assembly before
any wiring was completed, it looks much better than the standard mini
setup and will hopefully be more reliable and easier to trace faults if
they arise.
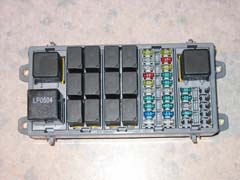
This is a picture after the wiring nightmare had been
completed on the back of the assembly. I've changed my mind about
making it easier to find faults :)
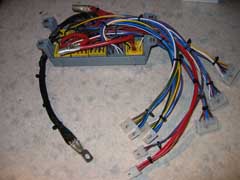
I was quite surprised to find that all the lights,
indicators and wipers worked first time as expected without any need for
changing the wiring plans at all. I guess all the time spent on
the design was worth it after all :) Looks quite a mess in the car
currently but it will all be tidied and hidden behind the dashboard
panels at a later date. Only the engine connections left to
complete now.
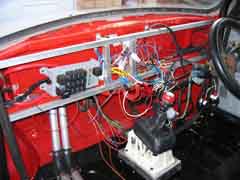
Thanks to the changes on the front bulkhead I am able to
install the battery in a handy location.
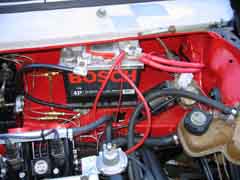
After the terrible wheelspin problems at the Mini
Showdown I decided to start work on the traction control unit earlier
than planned rather than go for slick type tyres or an LSD. The
control unit will work based on the RPM signals from both engines This is a picture of the early prototype which has yet
to be tested.
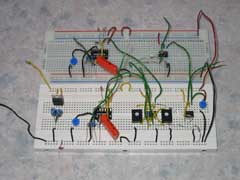
The prototype looks to be working as expected and i've
expanded slightly on the design by adding 3 led bar graphs which will
show the amount of slip on the front\rear and the threshold limit set.
This is a picture of the final circuits installed on stripboard but
still needing to complete the link wires from the bar graph LED's and
the stripboard itself needing to be trimmed into 3 separate parts.
I'm hoping to have this completed in time for Ten Of The Best 2006 which
is possible assuming it works first time out when installed in the car
:o)
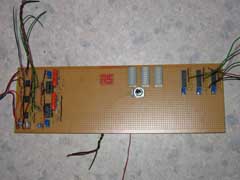
Once all connected up properly and cabled in the unit
looks quite qood.
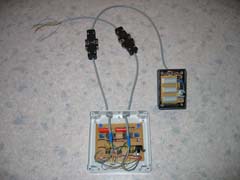
Still have the front face plate to finish for the LED
display part but other than that it is all completed. I have
briefly tested it in the car but only in neutral and by setting really
silly settings in the DTA which wouldn't be used on the road. The
result looks promising as it successfully cuts the ignition on the front
engine if the front rpm exceeds the threshold set compared to the rear
and the rear works the same also cutting if the rpm at the rear exceeds
the front. Quite by accident I've also found it to have a
secondary function as a flamer kit. The first field test will be
TOTB 2006 on Sunday now so here's hoping it all works as well as I hope
to get my 1/4 mile times down a bit lower :o)
After testing it has been found that a complete cut of
the ignition is too much and causes the car to bog down very badly.
Now instead of using the shift cut on the DTA i'm utilizing the launch
control input which uses ignition retard as the primary power control
and only resorts to ignition cut if this fails to control the wheelspin.
I only had a chance to test this briefly before the car was put away for
the winter but the initial test was very promising allowing a controlled
launch even in 1st gear :o) As you can see below the face plate
has also been completed.
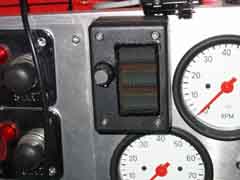
In order to monitor the a\f ratio accurately I have
installed front and rear wideband units, this provides useful
information during mapping and also monitoring capability when adding
the nitrous to the engines. The front unit is an early WBO1.5 unit
from Techedge, the rear unit is one of the much newer WBO2 DIY units
from Techedge which is capable of logging for up to 20 minutes and has
inputs for 3 exhaust temp probes, 3 general 5v inputs and RPM input.
Both units have outputs capable of connecting to the E48 ECU's to enable
closed loop control for lean cruise etc.
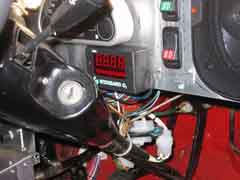
Front and Rear Engine Cooling\Heater
Installation
Although initially I installed both radiators in the
rear of the car for front space purposes it's proved to be insufficient
to cool both engines when running for longer periods of time due to the
same air flowing through the rear engine radiator after it has already
flowed through the front engine radiator. Due to this I have
redesigned the radiator setup with a front mounted radiator and a rear
mounted radiator.
In the front there is now a 2000 Renault Clio 1.9DCi
radiator with a 7" fan pulling air through the radiator and another 7"
fan pushing air through a different area of the radiator (this had to be
done as there simply wasn't space for a single large fan mounted on one
side of the radiator. Although this radiator is slightly smaller
in overall frontal area compared to the normal Vauxhall one it has the
fine meshed fin arrangement so should cool sufficiently due to the large
surface area of the cooling fins. In removing the front to rear
piping (along with the extra water in these pipes) I roughly estimate
that i've saved around 10kg's in ballast which should prove to be a
bonus.
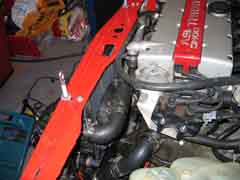
The rear engine now has the cooling fan to itself and I
have redone it to use the larger radiator that was used for the front
engine which was a South African Cavalier Turbo type and this has cooled
the front without problems.
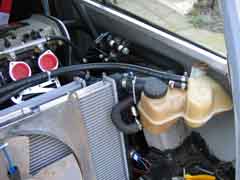
In order to remove the hot air from the rear engine
compartment I have made a fan cover that directs the air out under the
rear floor. I'm also hoping that there will be some vacuum effect
under the rear of the car so air will be drawn through the radiators
when cruising rather than the fan kicking in every 10mins or so.
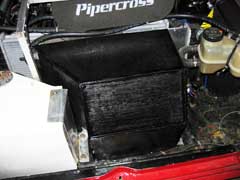
There appears to be too much air turbulence under the
boot floor to allow clean air flow from the radiator under the car so I
have made the rear valance a type of air duct in the hope that there
will be a partial vacuum at the rear of the car to draw the air through
the radiators. This involved basically cutting away some of the
rear valance and also drilling it behind the numberplate then boxing it
in using aluminum panels under the car to direct the air from under the
boot floor.
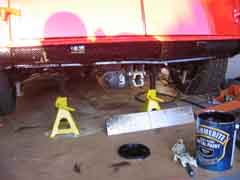
As I want this car to be fully road going rather than
just a straight racer I still needed a heater. In order to save
weight I decided to make a new lighter heater than the standard mini one
(which is pretty useless anyway). I used a standard mini heater
core, encased it in aluminum and used 2 high speed heavy duty PC fans to
supply the required air flow through the system. The new unit
weighs less than 1kg (without water) compared to approx 5kg for the
stock mini item, the fans will have 2 speeds available and on initial
testing seem to flow at least as much air as the stock mini setup.
The windscreen is due to be replaced by a heated version so there will
be no need for demist vents. The intake air will be supplied from the the
front of the car to avoid general condensation problems in wet \ damp
conditions. A late model mini heater valve will be installed in the
heater water pipes to provide the control of the heater temperature.
This is the basic lightweight heater core before
installation into the car.
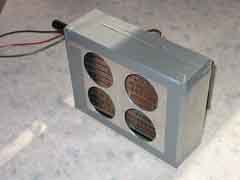
This is the new resting place of the heater core, quite
a tight fit so I will simply leave the vents to add hot air in the foot
wells rather than try and plumb in extra vents which really would be
more cosmetic than actually needed. As you can see i'm using the
later type mini heater water valve, when using this setup there also
needs to be a bypass pipe so that the water can still flow through when
the water flow to the core itself is shut off.
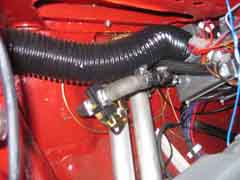
Front Engine QED Throttle Bodies and DTA
Management
This is the QED Direct to head throttle bodies installed
on the car along with the fuel rail, injectors, coil pack, adjustable
fuel pressure regulator and hoses. There won't be much detail in this
section as it deals with the bolt on aspect of the setup rather than the
tuning which has it's own section on the website.
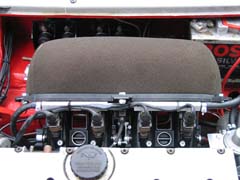
Here is the Jenvey throttle linkage and the DTA E48 ECU
before fitting to the car as you won't be able to see the linkage or the
ECU very well once fitted. I was originally going to design my own
throttle linkage but as I will need two identical setups for front and
rear I opted to purchase a ready built solution.
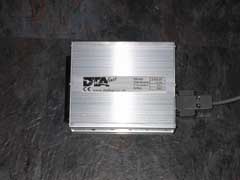
Managed to find a spot for the front and rear fuel pumps
that is fairly out of the way. The pumps are the same as the ones
used in the Jaguar XKR so should be able to provide ample fuel for my
requirements.
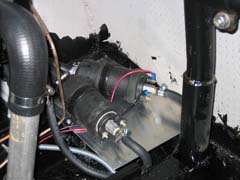
Dashboard Installation
Rather than lots of dials I have opted for the digital
dashboard solution for the primary items required by the MOT
(Speedometer, Warning Lamps, Odometer etc). I have installed
separate RPM gauges for each engine though as the dashboard would not be
able to provide information about both engines simultaneously. The
dashboard instruments are comprised of an ETB Digidash 2 Lite and 2x
80mm ETB RPM Gauges.
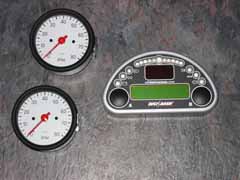
Here are a couple of pics of the initial install of the
dashboard in order to complete the MOT. Still a lot of work to go
though including the centre section by the gearstick for the heater
controls\radio, install the speakers, make a top cover and flock the
whole assembly so it looks a bit too stripped out racer in bare
aluminum.
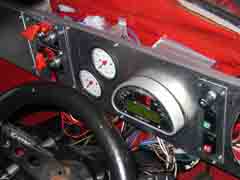
I have now moved the dashboard a little further from the
bulkhead to add a little sound proofing and also to allow more space for
wiring etc. Also I have now completed the gearstick surround and
the radio\heater control panel so almost looks like a proper dashboard
now with only the top cover to complete and then i'll be able to decide
on flocking the dashboard or carbon fibre effect. Only time will tell if
I can actually hear the radio over the engine noise :o)
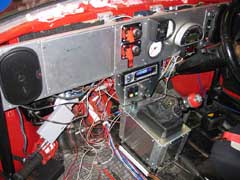
And finally a dashboard with a top so it's looking much
more normal now, still need to decide on carbon fibre or flock but that
will probably be next year now.
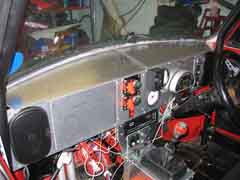
I've finally decided on a cover plan for completion over
next winter for the dashboard, will cover the main plates of the dash
with black flock and the smaller panels with switches etc will be re
made from thin carbon fibre sheet. I've also fitted a new steering
wheel as the old was was a bit on the rough side.
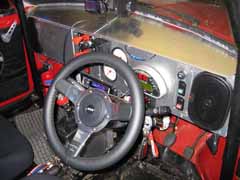
Handbrake Installation
As the handbrake needs to operate independently of the
main hydraulics for the MOT I have decided to install an extra set of
cable operated calipers at the rear rather than changing the main 4 pot
calipers for some combination hydraulic\cable calipers. This route
was chosen partially due to cost and also due to keeping the braking
system simple. The Wilwood mechanical calipers have been attached
to the rear of the hubs via some brackets which have been welded into
place.
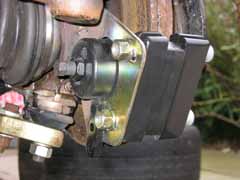
The calipers appear to work well, if you manually move
the lever the discs go quite stiff to turn. With more leverage
available using the proper handbrake lever they should be just enough
to pass the MOT requirements.
A handbrake cable from a modern vehicle was used rather
than the old mini type cable arrangement for ease of installation.
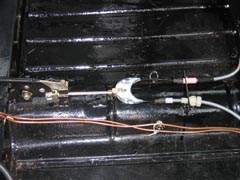
This handbrake setup proved to be very borderline on a
MOT test barely passing the minimum requirements, I think that the
problem was that there simply wasn't enough lever force being applied to
the caliper by the handbrake cable. This is now hopefully resolved
as i've extended the lever on the caliper so should have increased lever
force on the brake by about 2.5x, this should make the handbrake much
more effective.
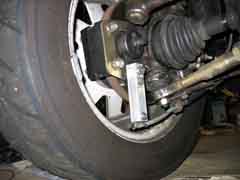
Cosmetic Changes to
Interior\Exterior
I really want to minimize the amount of visible changes
to the exterior of the car so it retains the original mini look.
There were some alterations which could not be avoided however.
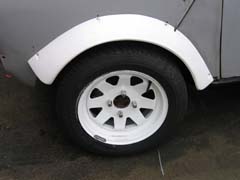
In the interior I have a couple of Sparco bucket seats,
these may be a little uncomfortable for long journeys so may be changed
for some sports recliners at a later time. Rather than use the
standard mini seatbelts I have purchased 4 point harnesses.
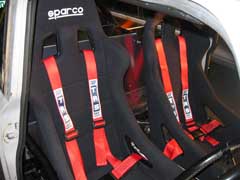
General Engine\Gearbox Upgrades
In order to increase the rev limit on the engines
(partially required to enable 60mph in 2nd gear but more for future
reliability) there are a few main components which need to be changed
from the factory standard to more suitable parts. (Of course all the
standard XE rebuild components were replaced as part of the job but not
detailed here as they were off the shelf GM parts such as water pump,
cam belt + idler pulleys, valve stem seals, gasket sets etc).
With these components installed the engines should be
able to rev safely to approx 8250rpm, any more than this would require
more replacement parts and becomes increasingly expensive which was to
be avoided where possible.
As these engines were of an unknown mileage (but at
least 15 years old either way) the oil pump was replaced. Rather than
use a standard replacement 20XE pump the one which is installed in the
more modern Z20LET was used. This Z20LET pump is capable of better
rpm stability as well as increased flow generally, it also utilizes
steel internal pump gears where the old XE pump uses plastic ones which
are known to break at high rpm. Visually they are virtually
identical apart from an extra lug at the top of the pump which needs to
be filed a little to clear the cam cover back plate and the centre seal
needs to be removed and replaced by one from an XE. (this is included as
part of the bottom end gasket set). Also with this pump the oil
pickup pipe needs to be created from scratch as the stock XE one does
not fit to the Z20LET pump, you cannot buy a direct fit one so you need
one from the Z20LET engine and then chop\weld to create one with the
same shape as the stock XE one.
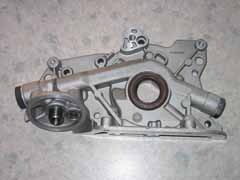
Again more for reliability under a most probable future
stressful life I have fitted some main\big end bearings which are of a
better compound than the stock items (stock being copper aluminum).
The main bearings are a lead copper mix and the big end bearings are the
Glyco 40 compound bearings which are a lead iridium mix, these Glyco 40
bearings are also 1mm wider than the current stock GM ones (GM used the
wider bearings in very early XE's).
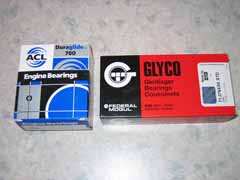
One of the weaker items when increasing the rpm limit on
the XE are the factory piston conrods\rod bolts. As these were now
very old and probably fatigued I opted to purchase some steel H pattern
rods which will be safe well above my required rpm limit, these also
came with arp 2000 rod bolts. Another bonus is that these each of
these rods weigh 110grams less (575grams compared to 685grams) than the
factory ones which should help also.
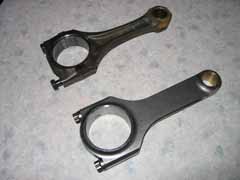
As I would like to see approx 210-220bhp normally
aspirated before adding any NOS it would require new cams and possible
head work, the XE valves are already close to the current piston valve
cutouts so while in bits thought it a good idea to have the pistons
machined to accommodate an extra 2mm of lift which should enable pretty
much any spec of cam to be used. I was originally not going to do
this but I found that the pistons were the earlier mahle forged items
rather than the later cast ones so a quite substantial amount stronger.
The original is on the left and the pocketed on is on the right.
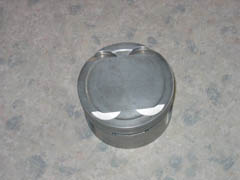
Fitting the exhausts would be interesting so say the
least as there's not that much room at the back for 2 systems. I
decided that I wouldn't have very large tailpipes as it would look wrong
and I also wanted to make the front system as quiet as possible but
still maintain the 2.5" bore. This was started off by installing 3
boxes in the transmission tunnel and then only a smaller box at the rear
due to space issues. The rear system will be very loud as even
though it has quite a large back box the distance from manifold to
tailpipe is only about 3 feet.
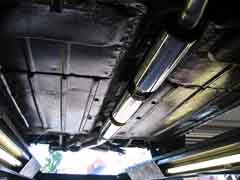 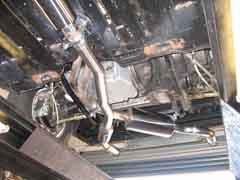 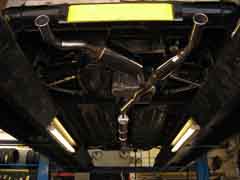
To improve the front end grip when coming out of corners
and also for drag racing I have now fitted a Quaife ATB Limited Slip
Differential, can't wait to give it a try on the strip now :o)
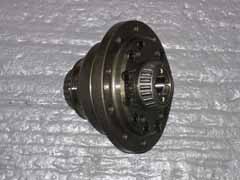
I may need to install another LSD in the rear eventually
but at the current power levels there really isn't any need and also
makes the car easier to get around corners with less chance of spinning
off as it will only break traction one wheel or the other at the rear
making the car safer on the road and track.
Rear Engine
QED Throttle Bodies and DTA Management
As the rear setup will be very similar to the front
there won't be too much detail here. This is a pic of the rear engine
with TB's installed and another with the filter installed ready to roll.
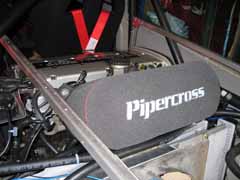
Nitrous Oxide Installation
Rather than just add the nitrous install to the end of
each engine section I thought it more fitting to have a complete section
just dedicated to the nitrous as it will be such a large key element of
the mini going forwards.
After much reading on the subject I decided to go with
the WON setup as this is really the only reliable setup that will
control the extra power delivered in a variable fashion, although
initially a direct fixed hit is fine eventually this will be changed to
a mappable\progressive setup as the extra power in increased.
First challenge was to find a space to install the NOS
bottle itself, this is a larger 11lb bottle as I expect that once i'm
running 2 engines on NOS it will use it up quite quickly and a 5lb
bottle would just be too small for the job. The only space I could
find that was suitable was to mount the bottle onto the rear rollcage
crossmembers, this makes it pretty visible from the outside (so much for
stealth lol) but does look like it means business :o)
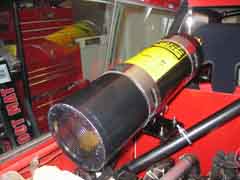
With only small trumpets on the intake (40mm) I opted to
fit the NOS Crossfire Injectors onto a bar that then allows them to
spray directly down the intake trumpets.
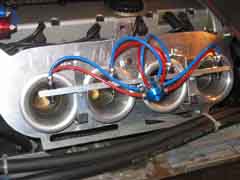
I added a few switches to control the NOS Bottle Heater,
NOS arming and at the same time a switch to enable\disable the traction
control.
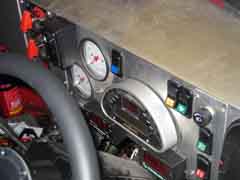
As we have such hot weather in the UK (NOT lol) I've
added a bottle heater to the setup in order to maintain a consistent NOS
pressure which avoids fuelling problems due to pressure fluctuations.
This heater automatically switches off at a bottle pressure of 950psi.
I also added a pressure gauge in order to check the pressure in
case of heat buildup in the rear engine compartment causing it to be too
high which could damage the engine from a lean condition being created
from too much NOS and not enough extra fuel.
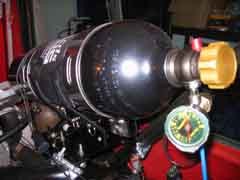
Fully installed at last, had a quick test and not that
much noticeable difference (could feel it just not a big kick in the
pants like you see in the movies lol) at the moment but that's with only
25hp on top of an already 340bhp so really a small hit in those terms.
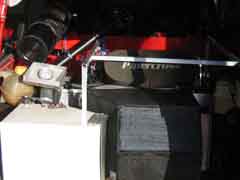
General
Bits'n'Bobs
I found a good spot for the windscreen washer bottle
just in front of the expansion tank, this is also a bottle from a
Vauxhall so holds more water than the mini one and also appears to have
quite a lot more flow and pressure from the built in pump.
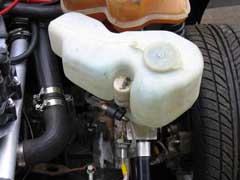
For the MOT (as well as looking decent) I have clamped
down all the fuel lines, Brake\Clutch lines and the wiring to the rear
of the car. Found that the electrical conduit from DIY stores was
perfect for the job. I have now relocated the fuel lines beneath
the car and used copper tube as the petrol smell in the car all the time
was not particularly good.
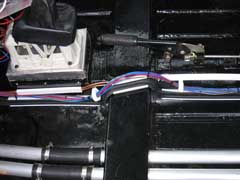
After the appalling grip problems experienced on the
drag strip and the street I decided that some grippier rubber was
required. After searching about I decided to try out the Toyo
888R's in a slightly wider 185 series than the normal Falken tyres which
were 175. As the profile had remained the same at 60 the overall
diameter has increased very slightly so should help with speeds
available in the gears. The other benefit of these tyres is that
they are V rated where all the other 13" ones were only H rated so
capable of a sustained 150mph where the H are only 130mph.
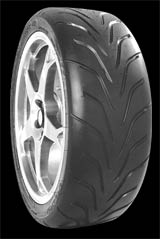
As the car had little or no good storage space attending a weekend show
with camping gear etc would prove quite difficult. I didn't want to
trailer the car to all the shows as the whole point of the car was to be
able to use it as a proper road car and cars that are taken on a trailer
to and from events I think are not really road cars anymore. To
address this storage shortcoming I have installed a towbar as I already
had a small trailer which could be used to store tools and camping gear
etc for shows. I didn't want it to be a permanently visible bar so
opted for a removable neck one and the install is quite hidden away when
the neck is removed.
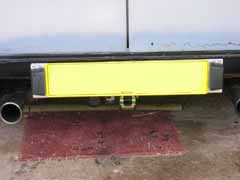
As I now had a slightly larger garage thought it was about time the mini
got a facelift :o)
Nice tango orange undercoat.
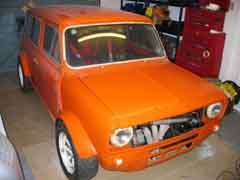
Finally in it's actual logbook colour.
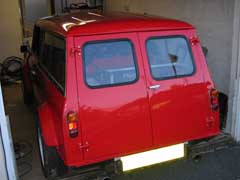
A fair while on and i'm having problems with the
suspension being too soft which has 2 effects, the first being that the
tyres can crash into the wheel arches and second that the large
suspension travel when accelerating\braking causes a larger bump steer
effect. To counter this i've ordered some much stronger springs
which are 500lb instead of 275lb which is the stock mini AVO
spring. Once this is done I expect that the car will sit too high
at the front so the spring will need adjusting to compensate, this would
be a problem as then when the suspension droops the spring will be loose
from the top seat and that is an MOT failure and could also be quite
dangerous. To fix this I have ordered some spring helpers that
take up the slack from suspension droop but are that soft that they have
no actual effect on the suspension otherwise.
These are the spring helpers
One of the new springs (yellow) alongside one of the old ones
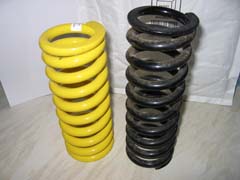
Another problem which was happening involved being unable to get gears
on the rear engine at racing events, it would work fine on the road then play
up at an event. After much annoyance constantly adjusting the
linkages it was found that the root problem appears to have been the
front engine moving around under load which upset the position of the
gearstick link to the rear gearbox. I have tried to counteract this by
fitting what seem to be much stronger engine mounts than the stock AMT
ones supplied. These new mounts are from Series 2 V8 Landrovers,
they are slightly larger diameter (only a few mm) and much less thick
(38mm compared to 50mm). Having less thickness improves their
stability as there is less rubber thickness to allow flexing however this
then required some 12mm spacers to bring them up to the correct
thickness so the engine would sit in the correct position, the rubber
itself also feels to be a harder compound. Here are the mounts
side by side with the new ones on the left. The engine can hardly
be seen to move now when driving with the bonnet off and the in car
vibration\noise hasn't noticeably changed.
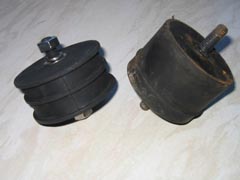
The new engine mounts were not strong enough on the front right of the
engine and ripped completely into 2 pieces. I've now made a new
mount from scratch using the middle of the ripped mount along with a cut
up mini thrust arm bush which has a bolt all the way through, I think
the bracket will break before this new mount and hopefully it won't make
the vibration transmitted into the shell too bad with the bushes top and
bottom of the mount.
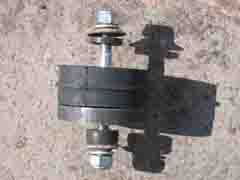
As was planning on some track sessions and maybe top speed runs now I
thought it may be a good idea to add a fire extinguisher for
emergencies.
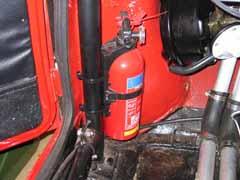
Although I now had full heating in the car one thing that is a major
problem on wet days is the windscreen steaming up, until now the only
solution was RainX AntiFog and a cloth to hand in case of steaming up
but now i've just fitted a heated windscreen to do the job. It's
of the modern type with very fine elements in that are barely
noticeable.
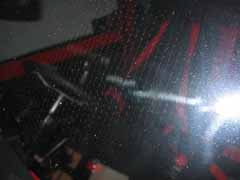
The front speakers were a little lacking in the volume department and I
had some spare 6x9's lying around so I fitted these in the back, not
much space left but they just fitted in there behind the seat under the
roll cage door bar joint. It's much easier to hear now when
travelling about and i've been able to reduce the crossover settings for
the front speakers so these cope better now too with less bass.
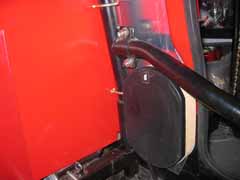
|