I decided to start a new build history section for 2
reasons, 1 being that the original build history was getting so large
and 2 that the change to automatic gearboxes would be quite large and
could get confusing with both the manual install and the automatic
install in one area.
(Click on pictures to see larger version)
F20 Manual and 4T40E Automatic Transmission General Information
The F20 gearbox is much smaller than the 4T40E Auto Transmission, the
4T40E Transmission itself was about the smallest Auto box I could find
that would even have a remote chance of fitting into the mini and also
be strong enough to take the current and future power from the engines.
The F20 would be at it's reliable limit at around 200hp where the stock
4T40E can take 250bhp easily. There are numerous upgrades
available for the 4T40E transmission that enable it to take 600hp+.
Another benefit of the auto box is the gear ratios are much more suited
to the mini's small diameter wheels, here is some comparison info of the
F20 and 4T40E in gear speeds.
|
4T40E mph |
F20 mph |
6500RPM \ Gear |
175\50x13 |
185\60x13 |
175\50x13 |
185\60x13 |
1st |
33 |
37 |
31 |
34 |
2nd |
61 |
67 |
51 |
55 |
3rd |
100 |
110 |
74 |
81 |
4th |
148 |
163 |
98 |
107 |
5th |
|
|
124 |
136 |
|
4T40E rpm |
F20 rpm |
|
175\50x13 |
185\60x13 |
175\50x13 |
185\60x13 |
Top Gear 70mph Cruising |
3100 |
2800 |
3700 |
3400 |
The reason the 4T40E would be an option was that the problem with most
auto transmissions is the width of the box from the engine block which
would totally make the install impossible due to the narrow nature of
the mini whereas the 4T40E box has the gears behind the engine with just
the primary torque converter and drop gears etc at the side of the block
making this transmission actually narrower than the F20. The rear
mounted gears wouldn't be such an issue at the rear but at the front I
expect some bulkhead modification may be needed along with moving the
steering rack somewhat. Another issue would be controlling
the automatic transmissions as they use virtually all electronic control
so would require ECUs and wiring where the F20 was simply mechanical.
F20
4T40E
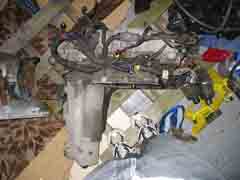
Engine Changes required to attach 4T40 transmission
The C20XE never came with an automatic option so in order to connect
this transmission to the engine I have needed to cut a small amount of
block away near the starter motor in order to clear the rear section of
the transmission and also will require a flexplate from a V6 C25XE or
X25XE engine to connect the crank to the torque converter.
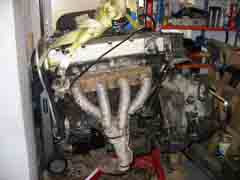
The flexplate was a bit of a nightmare, 1 to find any as they usually
get thrown away and 2 to make it fit. The V6 flexplate will only
fit correctly with the spacer included and then the bolt holes for the
torque converter didn't line up so I had to drill these myself, luckily
the accuracy of these bolt holes isn't very critical as they don't
perform any centering of the torque converter as this is done by the
shaft that fits inside the crank.
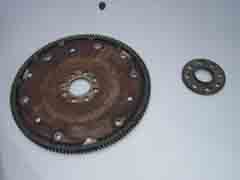
Electronics Required to Drive the Auto Transmissions
Along with the frame modification requirements the other biggest problem
will be controlling the auto transmission as these models are fully
electronic controlled, there are a couple of control units available in
the US which I will be investigating and will add the info as I find it.
After a large amount of checking into options for the transmission
control I am going to go with the TCM-2000 controller from PCS.
This was the 2nd most expensive controller I found but it has by far the
best features that are fully configurable for road, track and drag
modes.
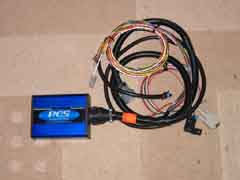
For the rear auto transmission I wanted to be able to run as before with
only the front engine in use. Although the 4T40E transmissions
support tow mode this is limited in range and also speeds that can be
used (100miles and more importantly 40mph due to the small mini wheels).
To counteract this limitation I needed to install an electronic pumping
system that would circulate the transmission oil to the bearings for
cooling\lubrication while the engine was off. There was a system
available in the US for this very job but at a cost of £500+vat and
shipping was expensive. A cheap similar version has now been
installed using a pump from a Nissan S14 200sx and 2 one way valves to
ensure the fluid flows the correct way around the transmission while
being electronically pumped or mechanically pumped.
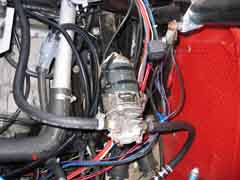
The PCS controller has many modes that are selectable including 2
completely separate base maps which can be selected electronically.
This switch enables switching between Map A (Normal Driving) and Map B
(Racing) also in the other position it enables sequential manual mode
utilizing the two buttons mounted on the steering wheel to select
up\down shifts manually for track use.
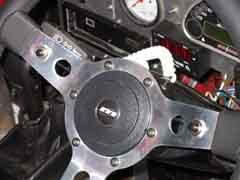
Drivetrain\Selector Changes As the 4T40E
Inner CV joints were a different spline pattern and also the shaft length
needed to be shorter I will require new driveshafts, I have two options
which are to chop\weld existing shafts to create new ones or to buy
custom one piece shafts. While the making shafts out of two pieces
may be cheaper overall I will be going with the new shaft route (mainly
for the strength\reliability aspect).
The shafts are somewhat shorter than the old AMT ones
and also much closer to equal length than before with no dummy shaft
required so I am hoping that torque steer will be reduced.
Original AMT shafts :- 350mm and 250mm
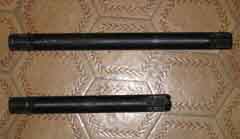
New Shafts :- 215mm and 267mm
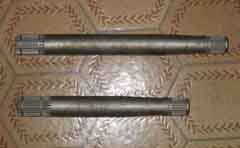
The new shafts are slightly thinner at the transmission end due to the
4T40E transmission compared to the F20 ones, I don't think this will be
a major problem since the original shafts used on the 4T40E were 1mm
thinner than these new ones, they used a lower grade steel and the
original cars that use this box have been running 360hp+ V6 Turbo's.
Although the transmission is virtually all electronic it still requires
a manual selector to engage Park, Neutral, Reverse and Forward Gears (I
think without any electronics at all it will run in limp mode as you
appear to get Reverse, Neutral and 3rd Gear when I tested the engine
earlier). To keep things simple for the front I have been able to
use the stock selector box and the original cable from the donor car
(it's a little on the long side but with a bit of bending around it just
fits). Rather than try to incorporate the rear engine into this
shifter I will create a new separate unit since there's no reason for a
single shifter as with the manual boxes (no need to shift apart from
selecting drive\reverse initially) and will make things more simple to
install.
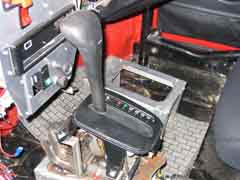
My existing dashboard wouldn't really fit around the stock selector so I
removed the upper plastic part and installed my old gear surround and
personally think is looks much better now although as a downside you
can't see which gear is now selected.
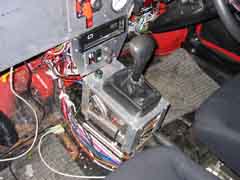
This is the gear selector for the rear transmission, as the auto boxes
are simply placed into Drive or reverse etc there was no need to have a
single unit that was connected for synchronous shifting. I will be
adding some sequential paddles to the steering wheel in the future for
track events etc and these will select gears on both transmissions at
the same time.
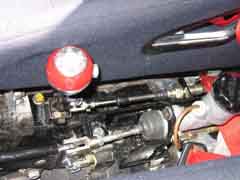
Rear Frame\Suspension Modification for Automatic Transmission Installation
The AMT frame has needed extensive changes to install the transmission,
many more changes that I had hoped were required. The main frame
lower section has needed to be widened by approx 30mm each side which
was difficult, a new side gearbox mount created in order to use the
stock gearbox mount (this will prob be better than the universal mount
used before) and a new set of rear mounts created. The driveshaft
connections sit slightly further back than the F20 necessitating a small
amount of cutting on the rear of the frame to clear the CV joints.
It does now just fit in there tho :o)
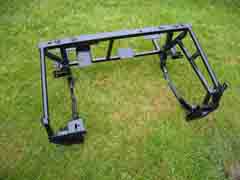
With the widening of the frame overall this would
obviously also widen the track of the car by approx 30mm per side, I
really didn't want a huge track needing huge wheel arches so I have
managed to shorten the suspension arm length by 10mm and also removed
the wheel spacers to get another 10mm however the wheels still protrude
beyond the arches so will require some slightly larger arches.
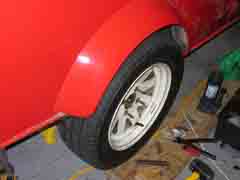
There is another problem which has become apparent in
that due to the shorter driveshafts the suspension cannot sit as high as
it did before or the driveshafts foul on the outer part of the inner CV
joints due to the angle of the driveshaft, in lowering the suspension
enough to combat this driveshaft angle issue it looks that will have to
return to stock mini size tyres (175/50x13) or have problems with the
tyres rubbing the arches even more than before. However as noted
above the gearing of the auto box negates the usual problems of too much
rpm when cruising but means another expense for new tyres which I hadn't
prepared for.
Front Frame\Suspension\Steering Modification for Automatic Transmission Installation
The front frame required similar modification to the
rear with the widening to clear the gearbox however the rear gearbox
mount needed to be different as there wasn't space to match the same
setup as was used on the rear. You can see that the rear mount
sits right in the corner of the frame at the back and I think that this
position may actually be stronger than the design of the mount for the
rear frame.
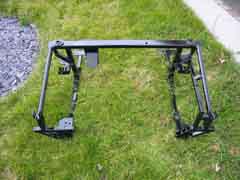
Similar changes were made to the suspension in line with
the changes to the rear.
The biggest issue at the front was the steering rack as
this was fouling on the back of the gearbox, in order to get around this
problem I had no choice but to move the steering rack approx 1.5"
downwards. Due to the angle of the panel where the rack is mounted
this has resulted in lowering the rack approx 0.75" and it now sits
approx 0.75" back. To try and combat any possible issues with
steering arm angles etc I am going to use the slightly longer metro arms
which also sit lower. Normally if widening the suspension pivot
points the rack would need to be widened in order to maintain the same
relative position between the upper and lower arms, with moving the rack
down this has returned the pivot points to near centre between the upper
and lower arms.
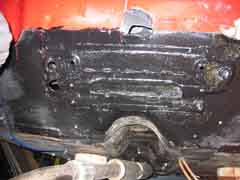
Due to the widening of the frame the steering rack arms
are no longer long enough to track the front wheels properly, I tried
the spitfire track rod ends which are longer than the stock mini ones
but they were only 1 thread on to get the wheels near straight so
another option was required. I looked into maybe getting a rack
from an Austin 1100\1300 as these are wider but use the same fitment and
steering column fitting but have a much lower ratio meaning more turns
lock to lock, where this would be good for holding on to it with torque
steer it needs to be decent for track sessions and loosing that much
steering ration would make it harder for track days. In order to
retain the stock rack part of the track rod arms were cut off, a decent
thickness tube was added so that approx 1/2" of thread was used of the
existing track rod and another 1/2" of thread was available to connect
an extension bar. This was very tight as by adding the joint
section the track rod ends are just able to be screwed in far enough to
create a little toe out (just needed some room for adjustment as when
the car is properly aligned it could require a little adjustment
compared to how it has been set by me) but can easily be adjusted now
for straight\toe in.
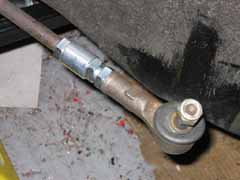
Further Performance
Enhancements
Now that the performance is consistent I can begin to
increase the available power until the limit of the transmissions or the
limit of grip is reached with the current setup. As there is
already a fixed nitrous shot of 50hp on the rear this can't really be
increased without risk increasing on the engine and transmission due to
the sudden torque increase. To improve on this situation and run
100hp+ of nitrous there needs to be a progressive controller available
to steadily increase the nitrous supply over a set period to limit the
shock to the engine and transmission.
Rather than purchase a ready made progressive solution I
decided to go down the DIY route which may not be as elegant or
professional as an off the shelf unit but much more rewarding (if it
works), more compact (I intend to integrate front and rear controllers
into one unit) and a lot less cost. I located a pre-tested circuit
diagram which has been successfully used by several people to control
nitrous and set about constructing the prototype.
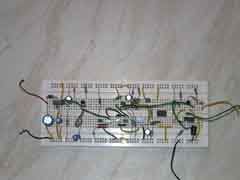
This single unit is functioning correctly on the bench
and has variable pulse frequency (10-100hz), start % (approx 10-40%),
build time (0.1-10 seconds) and max power (50-100%). Since
moving to the automatic transmissions I have decided that turbo power
would make sense since there is no need to lift off the throttle between
gears it will ensure no loss of boost pressure between gears. The
nitrous install will still come into play eventually but for the moment
is on hold.
The front transmission shift from 1st to 2nd gear is
resulting in traction loss due to the excess torque being dumped from
the engine at max rpm into 2nd gear. The current traction control
setup was using engine RPM for traction monitoring, while fine for the
manual setup this isn't really ideal for the automatic transmission
setup as there can be slight variances in RPM at the same speed due to
transmission slip, torque convertor tolerances etc. As a result of
this problem I will switch the traction control inputs to use the
transmission control unit speed outputs. Hopefully as these are
fully configurable pulse frequencies I will simply be able to rewire
from the old RPM signals to the speed outputs on the TCU's and
everything will behave as before. Another benefit of this setup is
that in the future as the engine power is increased I want to use
different shift points for each engine so the RPM would totally be
unsuitable in that situation.
I completed this work and it's performing perfectly
stopping all wheelspin within moments of breaking traction, required a
lot more changes than planned to make it work properly due to the larger
frequency range required for speed and also some signal damping to stop
small spikes causing the traction control to kick in.
General Changes \ Improvements
While completing this many changes to the Mini it was a
good time for a full tidy up of other areas such as suspension links
etc.
I was going to fit rose joint rubber boots but found
that really there isn't enough space for these on most of the joints so
changed my mind and left them off.
There was a small amount of play in the rear steering
arms and it was caused a little by the track rod ends, to help combat
this problem I have replaced the track rod ends with rose joints, this
simply required drilling out the hole in the steering arm on the hub to
1/2".
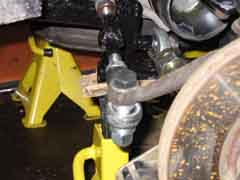
The handbrake setup is still far from efficient so to
improve this situation further and also lower the main rear brake
efficiency (even with the balance bar set max effort to the front the
rear still locks up before the front sometimes currently) I have
split the 4 pot rear calipers into separate halves so that the upper
pair of pistons will be used for a hydraulic handbrake assist and the
lower pair of pistons will work the primary braking effort. The
mechanical handbrake setup has to remain in place however as it's a
legal requirement for the handbrake to have a mechanical function but
the hydraulic part can assist.
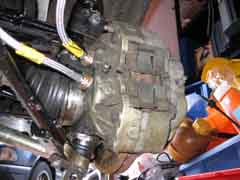
This setup feels much stronger than the mechanical one
as with only minor application of the handbrake lever you can't push the
car whatsoever and that's without the mechanical part currently
connected. :o)
Rather than just replace the tyres with the stock mini
size tyre I felt time for a change so opted to get a complete wheel\tyre
package so got a set of 6x13 Ultralites with Yokohama A539 tyres.
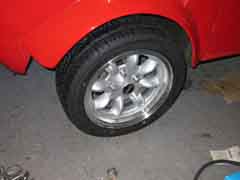
As you can see from the above picture the wheels stick
out beyond the arches so wider arches were required, I already had a set
of Watsons arches which weren't used during the initial build but they
were perfect for this job as they are about 3/4" wider than my current
ones. Still need to be painted etc but they are much stronger than
the old ones.
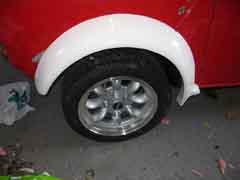
The automatic transmissions require cooling as opposed
to manual transmissions that rarely require a cooler, the front one was
simple as I already had a suitable radiator with the automatic
connections available but at the rear the large radiator i'm using
doesn't have this option. Rather than begin searching for yet
another radiator and another large spend (auto radiators are much more
expensive than a non-auto radiator) I have fabricated a cooler that will
install into the lower main water pipe. This is constructed from a
copper primary tube and then wrapped tightly with 10mm microbore copper
tube which is then soldered to the primary pipe for maximum heat
exchange.
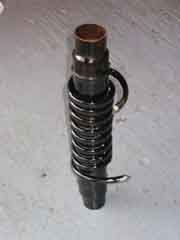
This heat exchanger will hopefully act in 2 ways, 1 to
cool the rear transmission on long journeys\racing and 2 to pre heat the
rear engine somewhat while travelling to a racing event saving on the
warmup time for the rear engine before racing.
The old fan cover didn't fit the new lighter fan
assembly so I made a new one out of aluminum this time.
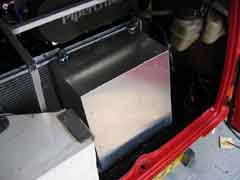
With the steering rack lowered the small stock mini
brake pedal was quite close to the column which wasn't comfortable to
use as your foot didn't sit well on the pedal. To improve the
situation i've fitted a larger brake pedal from OMP and it now feels
much more natural.
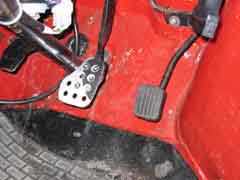
|